Industry 4.0 & its Revolution
Introduction to Industry 4.0
A new phase in the Industrial Revolution that introduces intelligent networking of machines and processes for industry with the help of information and communication technology.
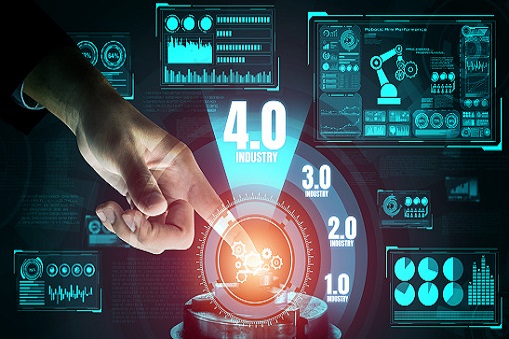
There is no easy way to become an actor or actress. But these are the most common steps for those who try to pursue a career path in acting industry. There are currently many film schools worldwide. Below are the Top 10 film schools in the world:
The term Industry 4.0 originated in 2011 from a project of German Government. It was first officially introduced by Executive Chairman of World Economic Forum Mr. Klaus Schwab in 2015.
Industry 4.0 will see many tasks that will ones performed by us, now being automated. With the collection and analysis of real time data, artificial intelligence, and the ability for all components of a production line to talk to each other, production can get really efficient and be personalized according to customer requirements.
What is Industry Revolution?
Industrial revolution is defined as the major changes and transition in manufacturing and industrial process with new innovative technologies. The evolutions of Industry Revolution are as follows:
- Industrial Revolution 1.0 (1784) - It started with the introduction of mass production by using water and steam power instead of purely human and animal power. The finished goods were built with machines instead of meticulously produced by hand.
- Industrial Revolution 2.0 (1870) - It started with the introduction of assembly lines and the use of oil, gas and electric power, along with more advanced communications via telephone and telegraph, that brought mass production and some degree of automation to manufacturing processes.
- Industrial Revolution 3.0 (1969) - It started with the introduction of computers, advanced telecommunications and data analysis to manufacturing processes. The factory digitization began by embedding programmable logic controllers (PLCs) into machinery to help automate some processes and collect and share the data.
- Industrial Revolution 4.0 (Today) - It started with the introduction of Cyber-Physical Systems by increasing automation and the employment of smart machines and smart factories, informed data helps to produce goods more efficiently and productively across the value chain. By collecting more & more data from the factory floor and combining those data’s with other enterprise operational data, a smart factory can achieve information transparency and better decisions.
What is Industry 4.0?
Industrial revolution is defined as the major changes and transition in manufacturing and industrial process with new innovative technologies. The evolutions of Industry Revolution are as follows:
With the help of Industry 4.0, our time will be used up in concentrating on more complex tasks. We will need a workforce who is capable of building, programming and developing these technologies. But also making sure we are applying them to our lives in and ethical way.
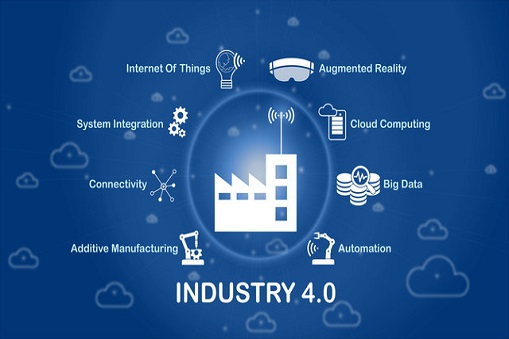
What technologies are driving Industry 4.0?
In Industry 4.0, computers, devices, machines are connected & communicate with one another to make decisions without human involvement. It helps in optimizing all existing digital technologies to next advanced level. The technology involved in Industry 4.0 includes:
- Internet of Things (IoT) - Internet of Things (IoT) is a vital component of smart factories. Machines on the floor of the factories are provisioned with sensors that feature an IP address which allows the machines to connect with other devices. This connecting mechanism makes it possible for large amounts of valuable data to be collected, analyzed and exchanged.
- System Integration - System integration is a process which is commonly used in the fields of engineering and information technology involving combination of various computing systems and software packages so as to create a larger system, and that's what drives the Industry 4.0 to work at its best. System integration is very useful in increasing the value of a system by creating new functionalities through the combination systems. Industry 4.0 takes into consideration all kinds of technologies, systems and machines, from smart phones and tablets to cars, white goods, web-enabled televisions, and more.
- Additive Manufacturing - Industry 4.0 is encouraging the integration of production systems and advanced information technologies. Additive manufacturing (AM) is considered to be a crucial ingredient in this new movement. The physical parts of the smart factory are bounded by the capability of the existing manufacturing systems which makes the AM as one of the key components of Industry 4.0. Due to the necessity for mass model in Industry 4.0, non-traditional manufacturing methods are needed to be developed. Thus, AM might become a key technology for fabricating customized products due to its ability to create advanced objects with advanced attributes (new materials, shapes). Now, AM is being used in various industries such as aerospace, biomedical, and manufacturing.
- Automation - The main goal of a connected factory is to maximize the efficiency, thereby maximizing profits. To achieve that efficiency and profit, automation must be embraced into some or all of the manufacturing processes. Automation is possible by the interconnectivity and communication that occurs across an industry 4.0 optimized facility.
- Bid Data & Data Analytics - Every function of the manufacturing operation is being monitored and generates data, there are tons of data to be shifted. As a result, big data analytics systems utilizes machine learning and AI technologies to quickly process the data's and give decision-makers the information they need to make improvements across an entire manufacturing operation.
- Cloud Computing - Cloud computing is the foundation of any Industry 4.0 strategy. Full awareness of smart manufacturing demands connectivity and integration of engineering, production, sales and distribution, and service. Cloud computing makes it possible. In addition to it, the large amount of data being stored and analyzed can be processed more efficiently and effectively with cloud. Cloud computing also reduces startup costs for small- and medium-sized companies who can right-size their needs and scale as their business grows.
- AI and Machine Learning - Artificial Intelligence and its subset of machine learning are a requirement for an Industry 4.0 smart factory. It allows manufacturing company to take full advantage of the volume of the generated information not just on the factory floor, but across their business units as well, and even from their partners and third-party sources. The whole thought around this new industrial revolution is to take out the manual labor, and AI is the primary tool to use in its place. AI can use the generated data from one factory to step up machinery, reprogram workflows, and identify overall improvements that can be useful in driving efficiencies and ultimately revenue.
- Cyber Security - Every touch point in manufacturing operation is connected & digitalized in industry 4.0, there is always an extra requirement for cybersecurity or cyber-physical systems. When there is a process undergoing a digital transformation to Industry 4.0, it is necessary to consider a cybersecurity approach that is used to encompass IT and OT equipment.
Advantages of Industry 4.0?
- Easy to do the backend integration with ERP/MES etc.
- It can be used to host micro services.
- It can be used for execution of transactions with soft real time.
- It is used for simple distribution of functionalities to multiple nodes.
- Easy to install, activate and change.
- Clear and monitored communication paths make resource management very simple.
- Easy to add new protocols and processes into industry 4.0.
- It is also possible to communicate between components on the floor.
Disadvantages of Industry 4.0?
- Companies are working to address the IoT security loop holes.
- Knowledge and Skills of the workers working on industry 4.0 projects need to improve.
- Because of redundant workers in corporate IT sector, adoption of industry 4.0 is a major threat for these workers.
- General reluctance to change to industry 4.0 by the company stakeholders.
- IT snags to be eliminated as this will cause costly production outages.
- Reliability and stability are required for M2M communication.
- It requires maintaining the integrity of production processes.
- It requires educating the staff to adopt the 4th industrial revolution which requires time as well as efforts across the industries.
Join Famark Community!
Famark community is a social platform for creative and innovative professionals from different domains.
Join Community